Revolutionary Alloy Developed at Lehigh University Stands Up to Extreme Heat
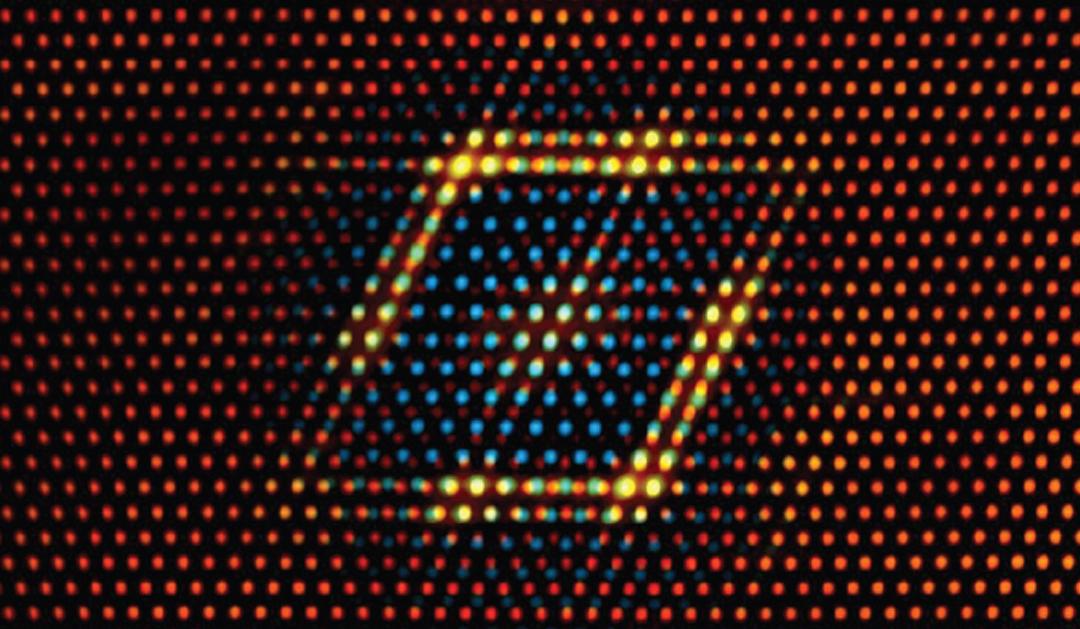
The Army Research Laboratory (ARL) and researchers from Lehigh University have joined forces with scientists from Arizona State University and Louisiana State University to create a groundbreaking alloy capable of enduring extreme heat without significant degradation. This innovative material represents a substantial leap in material science and could have profound implications for various advanced technological applications.
To facilitate ongoing research and development, Lehigh has recently upgraded its high-tech research laboratories, including the Nanoalloy Lab and Nanoceramics Lab. These state-of-the-art facilities are equipped with cutting-edge tools such as high-pressure torsion systems, nanoindentation equipment, and specialized high-temperature furnaces, allowing researchers to push the boundaries of alloy performance.
The recent breakthrough emerged from the unique formation of CuLi precipitates, which are stabilized by a tantalum-rich atomic bilayer complexion. This concept, pioneered by Lehigh researchers, diverges from typical grain boundaries that can migrate and destabilize under high temperatures. Instead, the complexion acts as a structural stabilizer, preserving the nanocrystalline structure of the alloy and preventing grain growth. This stabilization significantly enhances the material's high-temperature performance, allowing it to maintain its shape even under prolonged thermal exposure and mechanical stress, as noted by Patrick Cantwell, a research scientist at Lehigh University and co-author of the study.
By integrating the high-temperature resilience commonly found in nickel-based superalloys with the exceptional conductivity of copper, this new material holds promise for next-generation applications. Potential uses include heat exchangers, advanced propulsion systems, and thermal management solutions for cutting-edge missile and hypersonic technologies, which are critical in todays defense landscape.
This new alloy, identified as Cu-Ta-Li, provides a unique balance of properties that are not found in existing materials. Nickel-based superalloys, often utilized in jet engines, are incredibly strong but lack the thermal conductivity that copper alloys offer. Meanwhile, tungsten-based alloys are known for their impressive heat resistance but are also dense and challenging to manufacture. The Cu-Ta-Li alloy, however, successfully combines the exceptional heat and electrical conductivity of copper with the strength and stability required at extreme temperatures, positioning itself as a valuable complement to traditional superalloys rather than a direct replacement in ultra-high temperature applications.
The process of synthesizing and testing this alloy involved advanced techniques such as powder metallurgy combined with high-energy cryogenic milling to ensure a fine-scale nanostructure. The rigorous testing that followed included:
- 10,000 hours of annealing at 800C, which equates to over a year, to rigorously evaluate long-term stability.
- Advanced microscopy techniques that unveiled the intricate structure of the CuLi precipitates.
- Creep resistance experiments that confirmed the material's remarkable durability under extreme conditions.
- Computational modeling using density functional theory (DFT) to validate the pivotal stabilizing role of the Ta bilayer complexion.
Such an ambitious project is the result of years of meticulous work and collaboration, as highlighted by Christopher Marvel, a co-author of the study and a professor of mechanical engineering at Louisiana State University. Marvel emphasized how Lehigh's strong reputation in electron microscopy significantly contributed to the success of this material, stating, It was our microscopy that was really key to understanding the material. Marvels insights stem from his extensive six-year involvement in this research initiative, supported by his experience working on various high-level projects over the years.
The ARL has secured a U.S. patent (US 11,975,385 B2) for this innovative alloy, underscoring its strategic significance, especially in defense applications such as military heat exchangers, propulsion systems, and hypersonic vehicles. This development is just one of many fruitful collaborations between Lehigh University and the ARL, which have led to significant breakthroughs, publications in prestigious journals, award-winning poster presentations, and the successful placement of Lehigh students in esteemed fellowship programs.
Joshua Smeltzer, a Lehigh alumnus and now a design engineer at Honeywell, also played a critical role in this research. He performed advanced microstructural characterization of the superalloy using Lehigh's Atomic Resolution Microscope (ARM). Smeltzer remarked, Lehigh's ARM, a state-of-the-art electron microscope, is a unique instrument that enables scientists to analyze materials on the atomic scale. The ARM was instrumental in imaging the superalloy at both nano and atomic scales, providing essential insights into the mechanistic explanations for the alloy's exceptional performance.
Looking ahead, further research on this alloy will involve direct measurements of its thermal conductivity in comparison to nickel-based alternatives. Additionally, efforts will focus on preparing the alloy for practical applications and developing other high-temperature alloys that follow a similar design strategy. As noted by researcher Harmer, This project is a great example of how federal investment in fundamental science drives American leadership in materials technology. Scientific discoveries such as this are key to strengthening national security and fueling industrial innovation.
This remarkable advancement in materials science not only highlights the collaborative effort between academia and research institutions but also sheds light on the potential future applications that could arise from this innovative alloy, reinforcing the crucial role of materials technology in modern defense and industrial sectors.